Flexographic printing, commonly known as flex printing, is one of the most widely used methods for printing on various materials like plastic, foil, and paper. It is particularly common in packaging and label production, where high-quality output is essential. One of the key components of flex printing is the printing plate. A bad flexo plate can lead to several printing issues, from poor image quality to costly reprints.
In this article, we will discuss how to identify a bad plate in flex printing, the signs that indicate a plate is problematic, and how to address these issues to maintain consistent print quality.
What is a Flexo Printing Plate?
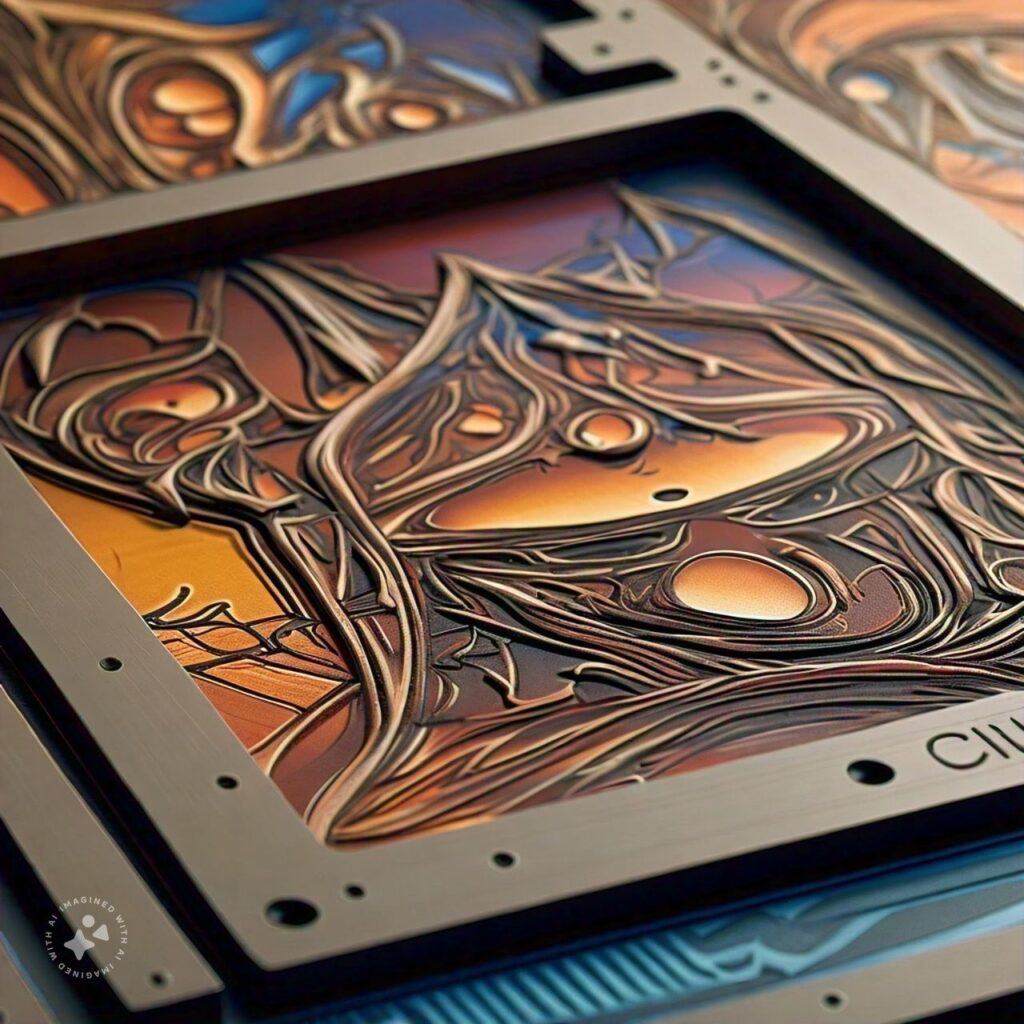
What is a Flexo Printing Plate?
Before diving into how to tell if a plate is bad, it’s important to understand what a flexo printing plate is and its role in the printing process. Flexographic printing plates are typically made of a flexible material like rubber or photopolymer and are used to transfer ink onto the substrate (e.g., plastic, paper, or cardboard).
The plate is wrapped around a printing cylinder and comes into contact with ink and the substrate, pressing the ink into the material to create the desired image or text. The quality of the plate is crucial for producing crisp, clear, and consistent prints.
If the plate is flawed, the print quality will suffer, leading to misprints, wasted materials, and dissatisfied clients.
Signs of a Bad Plate in Flex Printing
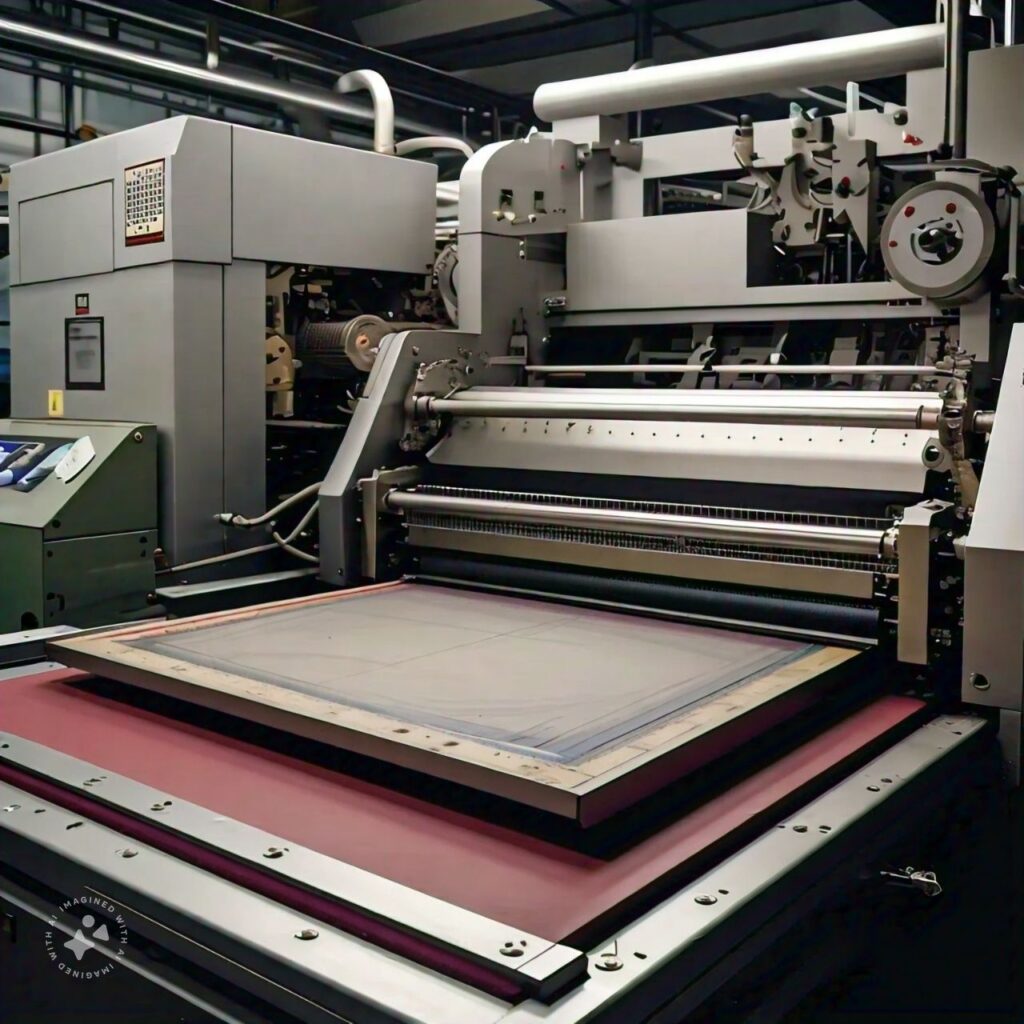
Signs of a Bad Plate in Flex Printing
A bad flexo printing plate can manifest in several ways, and recognizing the signs early can save you time and money. Here are the most common indicators that your plate might be problematic:
1. Uneven or Inconsistent Ink Transfer
One of the most apparent signs of a bad plate is uneven ink transfer onto the substrate. This issue can lead to prints that are patchy, faded, or uneven in color density.
- Cause: Uneven ink transfer can occur if the plate has been damaged, warped, or improperly mounted on the cylinder. Plate wear or improper cleaning can also contribute to this issue.
- Solution: Inspect the plate for any visible signs of damage, such as cracks or warping. Ensure that the plate is mounted correctly and that even pressure is applied across the entire surface. Regularly clean and maintain the plate to prevent ink buildup.
Also read: How to Value a Plumbing Business
2. Blurry or Fuzzy Print Quality
Blurriness or fuzzy edges in the print are often signs of a bad plate. Flex printing relies on precision, and any issue with the plate can distort the printed image or text.
- Cause: Blurry prints may be the result of a worn-out plate, incorrect pressure settings, or damage to the plate’s relief (the raised image or text on the plate). A plate that has stretched or lost its elasticity can also cause this issue.
- Solution: Check the plate for wear and tear, particularly in areas where intricate details are needed. Ensure that the printing press settings, including pressure, are optimized for the specific plate being used. If the plate is too old or damaged, consider replacing it.
3. Distorted Images
A bad plate can cause images to appear distorted, whether that means images are stretched, compressed, or misaligned. This can affect both the overall appearance of the print and the accuracy of brand logos, product designs, or other critical graphics.
- Cause: Image distortion is typically caused by improper plate mounting or by stretching the plate too much during the setup. If the plate is not securely fixed to the printing cylinder, it may shift during the printing process, leading to distortion.
- Solution: Re-examine how the plate is mounted on the cylinder, ensuring it is positioned correctly and securely. Avoid overstretching the plate, as this can cause permanent distortion over time. Use mounting tapes designed specifically for flexographic printing to prevent movement during printing.
4. Ghosting or Shadowing
Ghosting or shadowing occurs when a faint image of a previous print appears in subsequent prints. This can be particularly problematic when printing large runs, as it compromises the clarity and consistency of the final product.
- Cause: Ghosting often occurs when there is residual ink on the plate from previous prints. It may also be due to improper cleaning between runs or an overused plate that can no longer hold the proper amount of ink.
- Solution: Regularly clean the plate to remove any ink residue that could lead to ghosting. If ghosting persists, inspect the plate for signs of overuse or wear. Replacing the plate may be necessary to eliminate this issue.
5. Holes, Bubbles, or Imperfections on the Plate Surface
If you notice small holes, bubbles, or other imperfections on the surface of the plate, it’s a clear sign that the plate has been damaged or wasn’t created properly. These defects will lead to incomplete or flawed prints, with areas missing ink or showing uneven patterns.
- Cause: Imperfections in the plate can be caused by poor manufacturing, incorrect storage, or mishandling. Exposure to high heat, sharp objects, or chemicals can also damage the plate over time.
- Solution: Inspect plates carefully before each print run. Ensure that they are stored in a cool, dry place away from sharp objects or potential contaminants. If defects are found, replace the plate with a new, high-quality one from a trusted manufacturer.
6. Ink Buildup on Plate
Excessive ink buildup on a flexo plate is another common sign that something is wrong. This buildup can lead to clogged details, uneven printing, and eventual plate damage.
- Cause: Ink buildup can be caused by insufficient cleaning between print runs, using the wrong type of ink, or running the press at incorrect speeds or pressures.
- Solution: Implement a routine cleaning process for your plates between print jobs. Additionally, make sure that the correct ink type and viscosity are being used for your specific printing needs. Adjust press settings to minimize ink splatter or overflow.
7. Cracking or Breaking of the Plate
Over time, a flexo plate may develop cracks, particularly along the edges or areas with intricate designs. This is a clear sign of plate wear and a serious issue that will affect print quality.
- Cause: Plates can crack or break due to excessive use, exposure to extreme temperatures, or improper handling during mounting and cleaning. Repeated stress from the printing process can also cause plates to degrade over time.
- Solution: Replace cracked or broken plates immediately to avoid further print issues. To extend the life of your plates, handle them carefully during setup, cleaning, and storage. Avoid over-stretching plates during installation, and ensure they are kept in a stable, temperature-controlled environment.
How to Prevent Bad Flexographic Plates
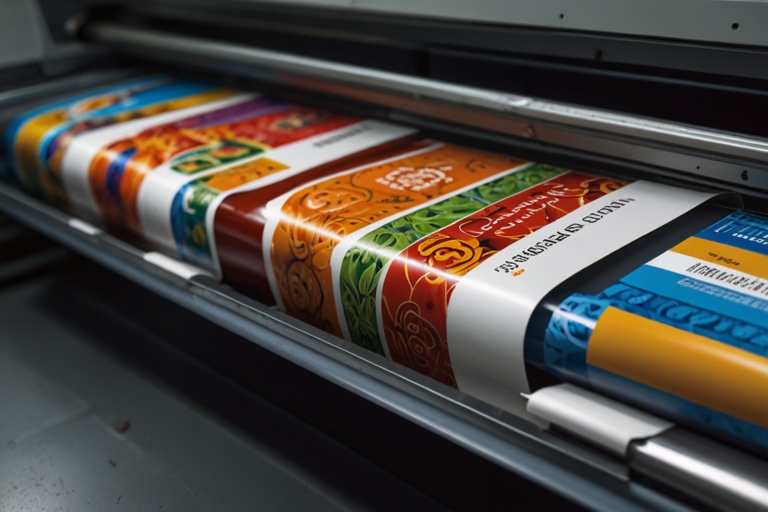
How to Prevent Bad Flexographic Plates
Maintaining high-quality printing plates is essential for consistent print output. Here are some tips for preventing bad flexo plates and ensuring smooth print runs:
1. Proper Storage
Store plates in a cool, dry, and clean environment. Avoid stacking plates directly on top of each other, as this can cause damage or warping. It’s recommended to use protective covers to shield plates from dust, moisture, and sunlight, all of which can degrade the plate’s material over time.
2. Regular Cleaning
Proper cleaning is critical to extending the life of your flexo plates. After each print run, remove ink and debris from the plate using specialized cleaning solutions designed for photopolymer or rubber plates. Be gentle when scrubbing, as harsh cleaning methods can damage the plate’s surface.
Also read: How to Print a Report Card in PowerSchool
3. Routine Inspections
Frequently inspect your plates for any signs of wear, cracking, or damage before starting a print job. This proactive approach allows you to catch potential issues early and replace bad plates before they can affect your print quality.
4. Use High-Quality Plates
Not all flexo plates are created equal. Invest in high-quality plates from reputable manufacturers to ensure better durability and print quality. Premium plates are often more resistant to wear and damage, leading to longer plate life and fewer print issues.
Conclusion
In flexographic printing, the quality of your printing plates plays a critical role in determining the success of your print job. A bad plate can lead to a host of problems, including uneven ink transfer, blurry images, ghosting, and more. By learning how to identify these issues early and implementing best practices for plate maintenance and storage, you can minimize downtime, reduce waste, and ensure that your prints meet the highest standards.
Understanding the key signs of a bad flexo plate and knowing how to prevent these problems will save your business time, money, and frustration in the long run.
Post Comment